Your CDMO Partner
for
We develop and manufacture your biopharmaceutical drug candidate – reliably and rapidly. Our innovative technologies can elevate your product to the highest yield, potency, quality, and safety levels.
Lenti.RiGHT® Production System
Rely on our Lenti.RiGHT® packaging and producer cell line as production system to unlock the full potential of your lentiviral vector construct. Choose what you need.
Take the Best Path to your Lentiviral Vector
The Lenti.RiGHT® packaging and producer cell line is well suited to produce lentiviral vectors in an efficient and reliable manner. This lentivirus production platform is based on our GMP-grade HEK 293 suspension cell, stably transfected with all required viral components. The inducible system enables a scalable and efficient production of high-titer lentiviral particles for various applications starting from early in vitro demonstration testing, preclinical studies, up to gene and cell therapies in a clinical environment.
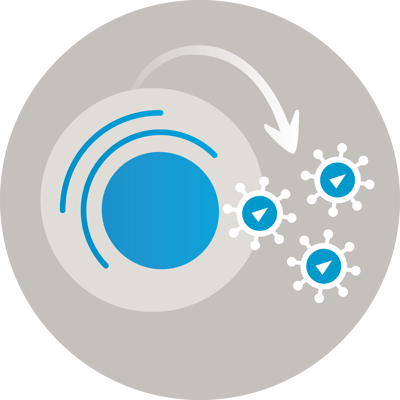
Key Features of Lenti.RiGHT®
Based on ProBioGen's suspension, HEK293 with superior growth characteristics in chemically defined medium that allows easy scale-up
Unique packaging cell clone with inducible gag-pol, rev and VSV-G genes located in best suited genomic spots
Proven long-term stability of Lenti.RiGHT® packaging cells due to the tight regulation system.
Lenti.RiGHT® Packaging Cell Line
Ideal Use Case: High-titer viral production for research and early clinical studies
Flexibility in Vector Design: Packaging cells without the stable integration of the lentiviral transfer vector allow for quick changes to the transfer vector, providing adaptability for different therapeutic applications.
Streamlined Process: This approach simplifies the production process by focusing on the generation of high-titer viral particles without the complications of integrating the lentiviral transfer vector into the packaging cell line.
High-Titer Production: These cells are optimized for high-titer viral production, making them suitable for producing sufficient quantities of vectors for research and early clinical studies.
Lenti.RiGHT® Producer Cell Line
Ideal Use Case: Later-phase clinical trials and commercial production
Consistency and Reproducibility: With all lentiviral packaging genes and the transfer vector stably integrated, these production cells ensure consistent vector production, critical for clinical applications where batch-to-batch variability must be minimized.
High Yield and Efficiency: These cells are engineered for optimal expression of all necessary components, leading to high-yield production suitable for large-scale manufacturing needed in later-phase clinical trials and commercial production.
Simplified Manufacturing: The stable integration of all components streamlines the manufacturing process, reducing the complexity and variability associated with transient transfections and ensuring a more robust production pipeline.
Cost-Effectiveness: Over time, the use of these stable production cell lines can be more cost-effective due to reduced variability, elimination of the need for repeated transfections, and consistent high yields, leading to lower overall production costs.Transient Transfection
Ideal Use Case: Early Phase Clinical Trial
Rapid Production Cycle: Transient transfection allows for the rapid production of lentiviral vectors, making it ideal for applications requiring quick turnaround times, such as early-phase clinical trials or urgent research needs.
Flexibility: This method provides high flexibility in changing vector designs and incorporating genetic modifications. Researchers can easily adapt to different constructs without the need for long development cycles.
Scalability: Though traditionally seen as less scalable than stable cell lines, advancements in transient transfection techniques have significantly improved yields, making it feasible for larger-scale productions.
Reduced Development Time: Bypassing the need for generating stable cell lines cuts down on the time required to initiate production, enabling faster project initiation and delivery.
Benefit from using Lenti.RiGHT® as Production System
High Flexibility
High Process Stability
Easy Scale-up Possible
Flexible CDMO Services to Develop and Manufacture Lentiviral Vectors
Whether you want to develop your lentiviral vector by transient transfection, packaging or producer cell line - whether you also need process development and GMP compliant manufacturing - we can help you!
We offer End-to-End CDMO Services to develop and manufacture lentiviral vectors based on our packaging and producer cell line Lenti.RiGHT. We can produce the virus as starting material for cell therapy and/or a Lentivirus as drug product. In any case we help you unlock the potential of your lentiviral vector construct.
Vector Design and Development
-
Lentiviral Production with either Transient Transfection or Lenti.RiGHT as Production System
- Stable insertion of the ‘gene of interest’ (GOI) in combination with DirectedLuck® transposase
- Generation of cell clones capable to produce highest titers
- Testing of genetic stability by performing long-term passaging experiments including Next Generation Sequencing (NGS) techniques
Process Development (DSP/USP)
- Customized Solutions: Tailored to specific product needs.
- Advanced Filtration Technologies: Enhances purity and safety.
- State-of-the-Art Chromatographic Systems: Ensures high yield and precise purification.
- Process Efficiency: Maximizes recovery and minimizes production time and costs.
- Process development in respect of the route of drug administration for Upstream and Downstream Processes
- Thorough screening for best conditions in terms of lentiviral yield and reproducibility
- Lentiviral production development in various scales and reactor types including but not limited to:
- Wave, Orbital Shaken and Stirred Tank Bioreactors
- applications and chromatographic purification methods using latest chromatographic systems
GMP Manufacturing
- Versatility in Scale-Up: Supports small to large-scale production (up to 200L scale in stirred tank bioreactors).
- Reactor Flexibility: Adapts to different bioreactor types for optimal production.
- Process Robustness: Maintains high yield and quality across scales and reactor types.
- Manufacturing of drug substance and drug product fulfilling requirements specified in EU GMP Annex 1
- Tailor-made purification and formulation process depending on your needs
Analytics, Bioassay & Quality Control
- Functional Titer: Detection of provirus integration by ddPCR ensures vector functionality.
- Gene Product Expression: Assessed at protein (flow cytometry) and RNA (ddPCR) levels.
- Physical Particle Titer: Measured by p24 Gag ELISA for accurate viral particle count.
- Physical Genomic Particle Titer: Quantified by ddPCR or RT-PCR to assess genomic RNA.
- RCL Detection: Ensures the absence of replication-competent lentiviruses.
- Integration Profile: Analyzed by NGS for comprehensive safety and predictability.
- Sterility Test: Ensures sterility of production runs.
- Host Cell DNA and Protein Assays: Quantification ensures minimal residuals.
- Mycoplasma and Endotoxin Tests: Ensures absence of contaminants and low endotoxin levels.
Elevate Your Candidate With The Right CDMO
ProBioGen - Your Integrated CDMO and Technology Expert for Biologics and Advanced Therapies
ProBioGen is a Berlin-based specialist for developing and manufacturing biopharmaceutical active ingredients, viral vectors and vaccines with applying proprietary technologies to improve product quality and features. Combining both state-of-the-art development services, together with intelligent product-specific technologies yields biologics with optimized properties. Rapid and integrated cell line and process development, comprehensive analytical development and GMP-compliant manufacturing is performed by a highly skilled and experienced team.
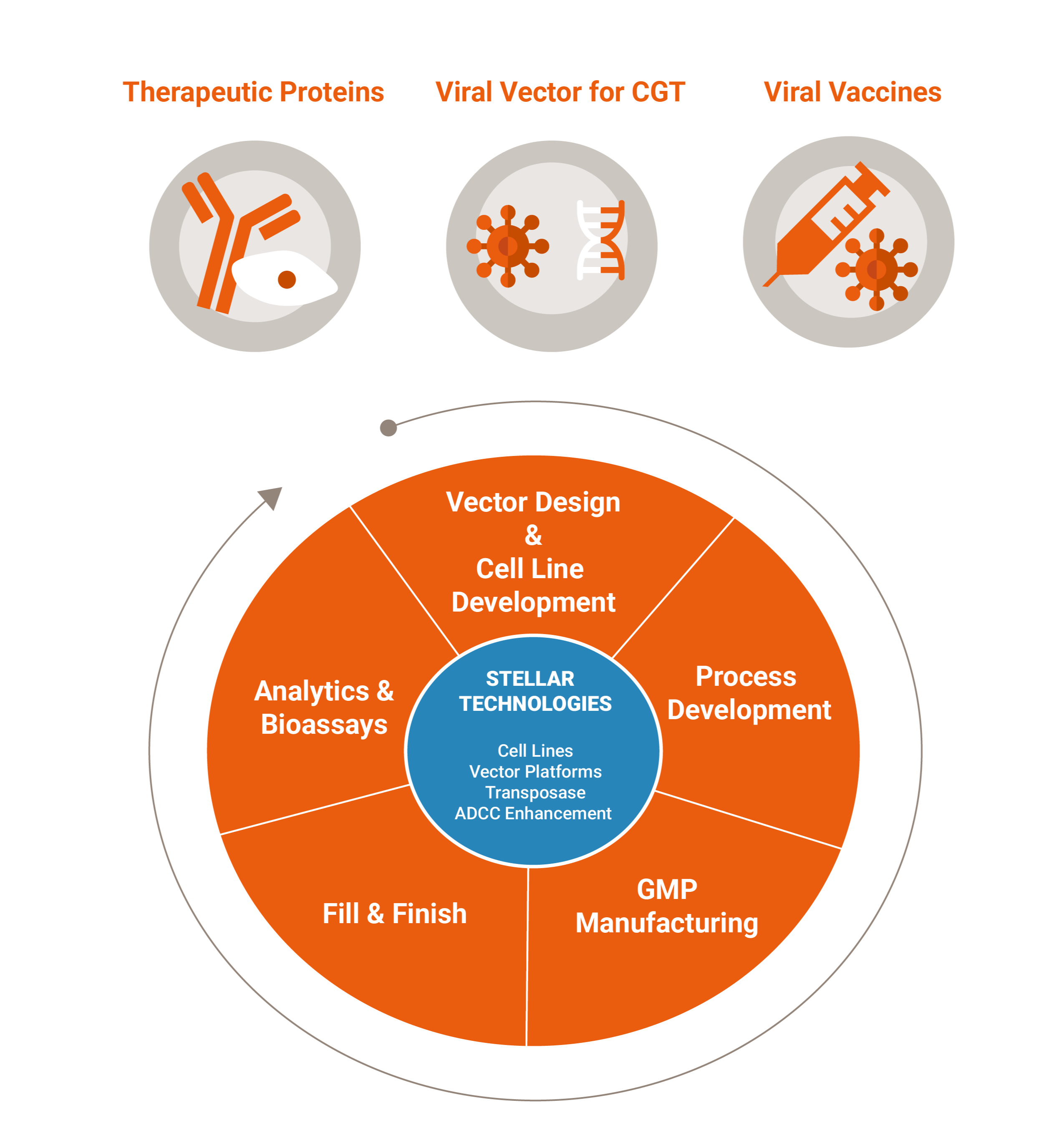